ATLAS EMBARKS ON AN EPIC VOYAGE TO REPAIR CRUISE SHIP
When a cruise ship needed a repair to their Generator Thruster Shaft, the Atlas on-site Field Machining team was there to help.
A CRITICAL REPAIR
In the world of field machining, time is often of the essence, and precision is paramount. A testament to this fact is the remarkable repair operation carried out by Atlas, a renowned field machining service provider, on a cruise ship. Facing a critical repair request to fix a generator thruster shaft, Atlas rose to the challenge, showcasing its dedication to excellence and customer satisfaction. This repair project was vital for the cruise ship. The thruster generators are indispensable for safe porting and departure, and without them, the ship could face operational difficulties at various ports or may not be allowed to port at all.
Before Atlas
After Atlas
OVERCOMING CHALLENGES
Atlas understands urgency. Our solution-oriented technicians are able to tackle any job quickly. The ship had four thruster generators, which played a pivotal role in guiding the vessel during porting and departure. If one of these units failed, the ship would not be able to port at some locations, which required all four thrusters to be in working order.
The repair job had to be performed three flights below the ship's deck, below sea level.
This location not only posed technical challenges but also the possibility of motion sickness for the Atlas crew. With over a century of knowledge behind us, Atlas was able to expertly prepare by ensuring all safety measures were met and equipment was shipped to the site prior to arrival.
Finding a company that can repair on-site and has the technical knowledge/skills to repair it correctly the first time can be a difficult task. For this project, Atlas had to design and manufacture a specialized sleeve to be installed on-site and had to ensure the straightness of the shaft before executing the repair. Atlas’s expertise and quality design ensured the repair was completed correctly and efficiently.
ATLAS ACTED FAST
The initial request came in on Thursday, October 13, 2022, when Atlas received a call from the operators of the cruise ship. The customer's request was straightforward: they needed a repair on a critical component – a thruster generator shaft. Atlas wasted no time. On October 14th, they came up with a repair plan. The following day, they designed the sleeve that would be installed on-site. By October 18th, the sleeve was manufactured, and equipment was enroute to the port. The crew arrived on October 22nd, and on October 23rd, they boarded the ship with the necessary equipment. The Atlas team was not just there to repair; they went above and beyond. They machined and installed the sleeve and even assisted the ship's crew in assembling the thruster generator. The Atlas crew remained on board the ship until it reached its destination in Fort Lauderdale, Florida, on October 29th.
A TESTAMENT TO EXCELLENCE
The repair of the generator thruster shaft on the cruise ship serves as a testament to the commitment and expertise of Atlas in the field of field machining. This remarkable feat not only highlights the importance of precision and timeliness but also underscores the critical role that specialized services play in keeping industries like cruise ships operating smoothly. Atlas's dedication to going above and beyond for their customers is a shining example of excellence in the field.
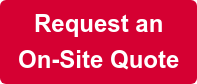